Compatibility Of Chemical Admixtures With Cement
Last week, I went to a client’s site because they had been having trouble making concrete for a few days and asked me to check things out. I kept wondering what might have gone wrong and what problems they were having. I learned that pipelines choke, concrete appears to be flowable but it’s settling, concrete is workable while producing but abruptly drops, and other things. None of them have taken an effort to understand why it’s happening, even though they have outlined the practical difficulties they have encountered.
As I dug deeper into the problem, I learned that the cement brand had been changed for the past two days due to a shortage of the original brand. Despite the fact that the admixture was the same as it had been for a long time, this new cement brand has caused a number of problems for the company. I discovered this and let them know there was a compatibility problem. I went on to say that different brands of cement and admixture won’t perform the same even when they adhere to the relevant codal requirements, which leads to serious incompatibility problems such flash setting, delayed setting, rapid slump loss, cracking, and aberrant strength gain pattern.
The compatibility of an admixture with cement is affected by a number of factors, including:
- Cement’s fineness (Amount of admixture will be more for finer cement due to availability of larger surface area of cement particles)
- The chemical makeup of cement, particularly C3A (When C3A is high but availability of sulphate is low, this causes rapid slump loss)
- The composition of the calcium sulphates used in cement grinding
- Concreting temperature
- Type of admixtures (Chemical family like Ligno, SNF, PCE, chain length of polymer, molecular weight of polymer and dosage of admixture)

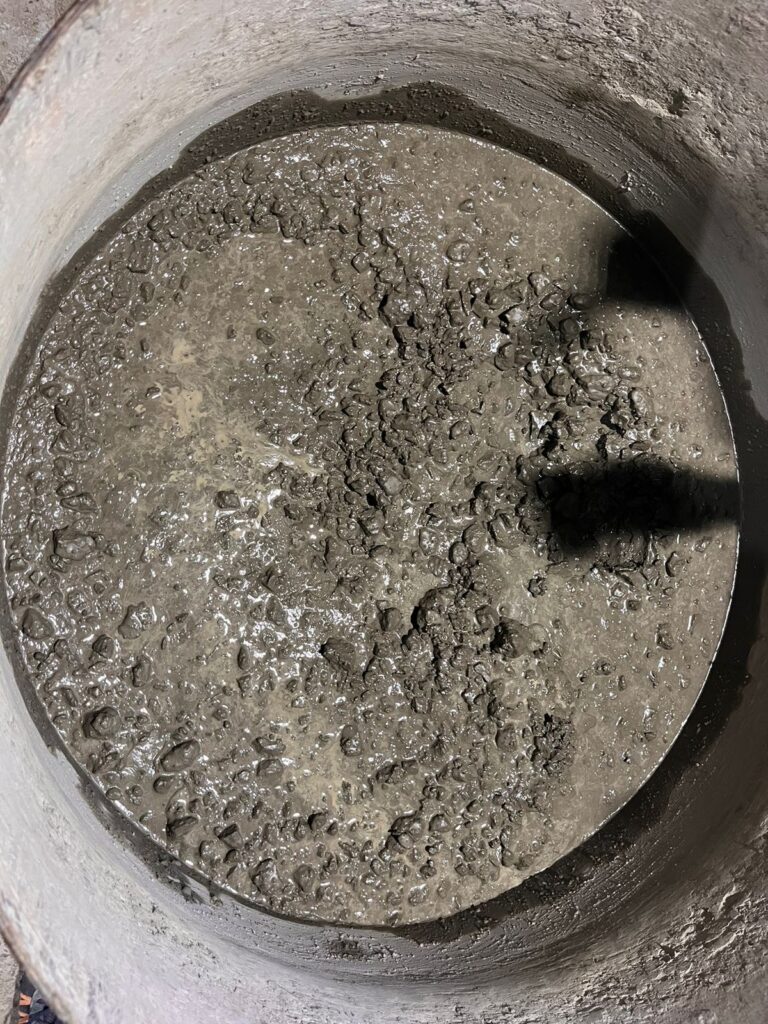
The Marsh cone test is a quick and easy way to determine whether an additive and cement are compatible. The behavior of cement paste is described. This test measures the amount of time required for a specific amount of material to flow out of the cone. The fluidity of the material under test is related to this measured flow time. The fluidity decreases as the flow time increases. This test can also determine the admixture’s optimum dosage, which is the amount below which slump loss and flash set are detected and above which delayed set and segregation may occur without a noticeably reduced flow time.
Therefore, whenever we switch the brand of either the cement or the admixture, a compatibility test must be performed to ensure that the admixture is compatible with the specific brand of cement and to determine the ideal dosage of admixture to be used in the concrete for the desired work-ability, strength, and durability.
Let’s educate the people around us.!
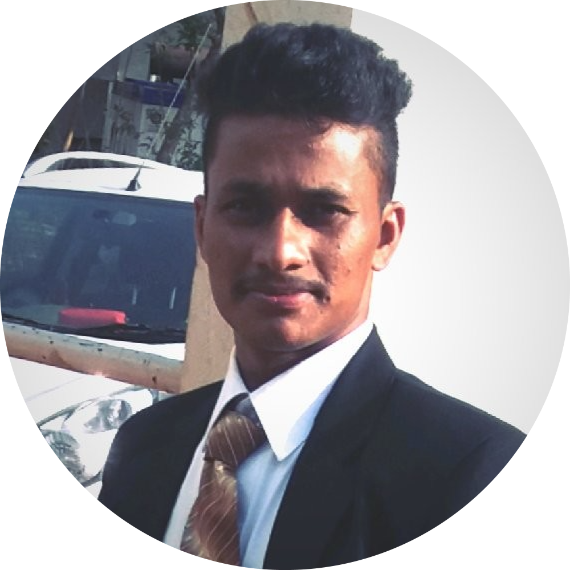
Daud Hipparagi
Deputy Manager – Concrete Technology at Infra.Market | RMCMA Certified Concrete Technologist | MBA – Marketing | Construction Chemicals | Admixtures | RMC |